
An industrial robot guides the hemming roller and forms the flange. Roll hemming is carried out incrementally with a hemming roller. Production plants for conventional die hemming are very expensive, but the cycle times are very low. These steps include, for example, the pre-hemming and final hemming depending on the respective opening angle of the flange. The formed flange is then hemmed in several process steps. Normally the actual hemming is a result of a forming operation in which the flange is formed with a hemming tool after the drawing and trimming operations have been completed. In die hemming, the flange is folded over the entire length with a hemming tool. There are various types of hemming operations:Ĭonventional die hemming is suitable for mass production. This is why it is important to use simulation tools in order to, on the one hand, better understand the hemming process and, on the other hand, significantly reduce the number of “trial and error” loops during tryout und production. Typical hemming defects are splits or wrinkles in the flange, material overlaps in the corner areas or material roll-in. Material deformations, which occur during the hemming process, can lead to dimensional variations and other defects in parts. The accuracy of the hemming operation is very important since it affects the appearance of the surface and surface quality. Typical parts for this type of assembly are hoods, doors, trunk lids and fenders. In car part production, hemming is used in assembly as a secondary operation after deep drawing, trimming and flanging operations to join two sheet metal parts (outer and inner) together.

Normally hemming operations are used to connect parts together, to improve the appearance of a part and to reinforce part edges.
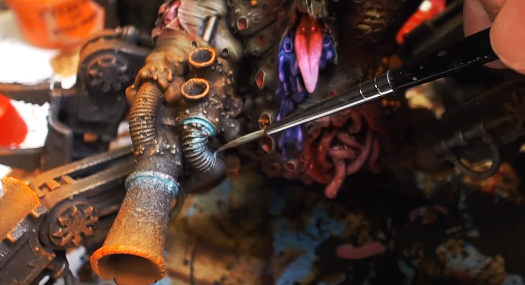
Hemming is a forming operation in which the edges of the sheet are folded or folded over another part in order to achieve a tight fit.
